Aggregate Industries delivers record concrete pours at Longhill Burn wind farm project
Aggregate Industries has proven its unrivalled logistical prowess once again, having completed a record 750m3 weekly concrete pours over the course of eight weeks to support the turbine infrastructure of Scotland’s landmark new multi-million pound wind farm: Longhill Burn.
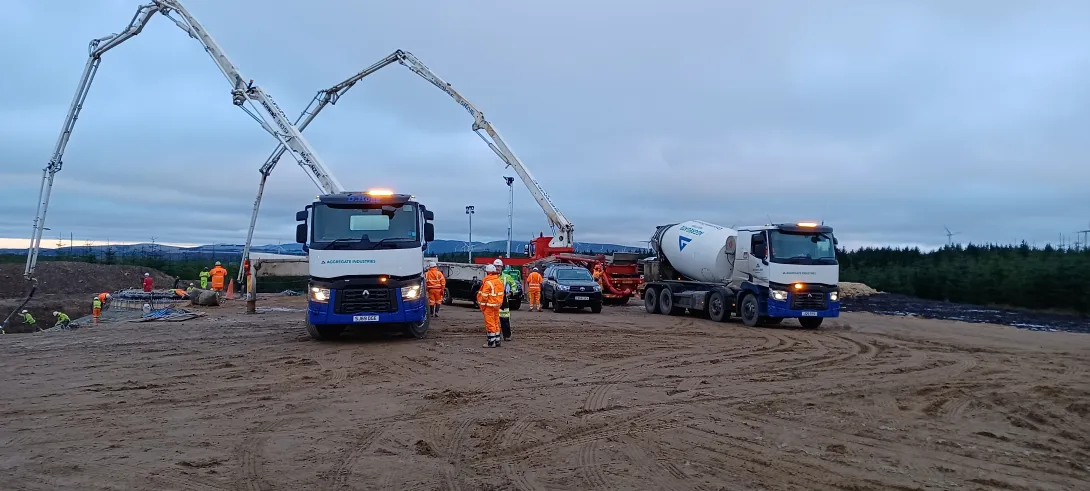
The Longhill Burn project is a new multi-million pound wind farm that has been built in West Lothian, Scotland. Once completed, the 50MW wind farm will comprise eight of the largest available capacity onshore turbines and is expected to be one of the biggest subsidy-free onshore wind projects in the UK once operational.
Core to the wind farm’s foundational structure, awarded contractors A E Yates sought a specialist partner with the ability to supply and pour the vast 750m3 concrete requirement for each of the eight wind turbine bases at a rate of approximately one per week, in line with the
wider project’s meticulous framework.
Given the sheer scale of the project, it was equally important that the concrete specification be purposefully designed to incorporate blended cement to reduce the associated heat created by large volume pours. No easy feat, this came against the backdrop of a highly remote location and limited local transport amenities.
Chosen for its unrivalled pedigree in large scale concrete pours and local access, Aggregate Industries’ response was a holistic one. Recognising that the weekly 750m3 quota was too large for one single local plant to fulfil, the team devised a robust delivery framework with the main supply provided by the business’ nearby Duntilland plant.
Its nearby Ratho plant was then on standby as backup. This was supported by Aggregate Industries’ Grangemouth and Coatbridge plants which were deployed to send supplementary loads as required.
Equally innovative was the team’s approach to product. Each pour consisted of a bespoke blend of CEM 1 and Ground Granulated Blast-furnace Slag (GGBS) specifically designed to reduce the temperature rise and help to avoid early-age thermal cracking otherwise inherent
in huge volume pours.
Sustainability was accounted for too, with the unique blend categorised within Aggregate Industries’ market leading ECOPact green concrete range, which offers 50 per cent carbon reduction when compared to traditional solutions, while ensuring the same setting time and structural performance.
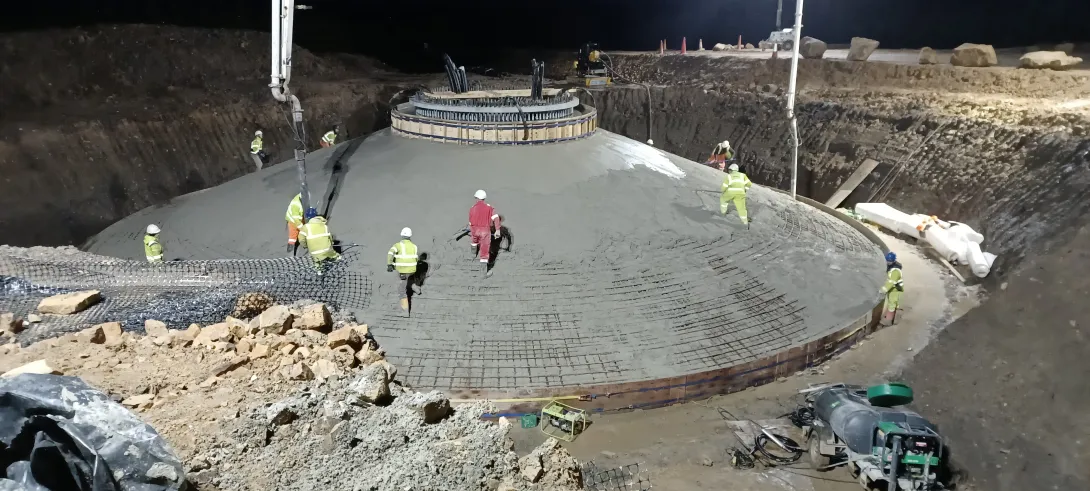
Alongside providing cutting-edge innovation, a key component of Aggregate Industries’ success with the project was its remarkable speed of delivery.
Within a total weekly window of approximately just 12 hours, the team was able to complete each weekly quota, in accordance with available driver hours. This was supported with a team of 32, including, amongst others, four shippers, six production staff, two technical experts and the entire Scottish ready mix concrete driver fleet.
In total, the specification included 6080m3 of ECOPact Prime and 700m3 of general concrete as well as 21,500 tonnes of aggregates and 1,300 tonnes of sand.
John Young, customer services manager at Aggregate Industries, said: “The Longhill Burn wind farm project is a nationally defining one which will set the benchmark for opportunities to decarbonise energy supply as we address the challenges of climate change and energy security.
"We are therefore very proud to have secured this competitive contract which, we believe, is a reflection of our leading capabilities, both technically and strategically.
“Logistically, this was a challenging contract. It meant we had to keep two pumps active at all times, with our entire Scottish team working tirelessly behind the scenes to ensure all pours were completed. It also required an incredibly tight-knit approach to shipping and delivery, making sure we were able to make exacting slots.
"In terms of the product itself too, we were able to provide a bespoke solution as well as guarantee first-class structural performance and 50 per cent carbon reductions. However, thanks to our local presence, product innovation, precise planning and sheer hard work, we are immensely proud to have delivered on all counts.”
Press contacts
-
Telephone
01530 510066
-
Email
“Logistically, this was a challenging contract. It meant we had to keep two pumps active at all times, with our entire Scottish team working tirelessly behind the scenes to ensure all pours were completed."
- Major framework win for Surfacing Solutions in Scottish capital
- Aggregate Industries launches the industry’s first carbon reporting tool to offer customers accurate carbon data by product or project
- Aggregate Industries launches ambitious 2030 sustainability strategy: Building Progress for a Sustainable Future
- Innovative SuperLow Carbon wins top industry award
- Aggregate Industries expands its low carbon concrete product range with the launch of ECOPact Prime AS
- Aggregate Industries switches to warm mix asphalt as it continues with sustainability pledge