net zero hero dave champions energy efficiency
As part of our ongoing focus on how everyone across Aggregate Industries can play a part in helping achieve zero emissions before 2050 we speak to our latest Net Zero Hero.
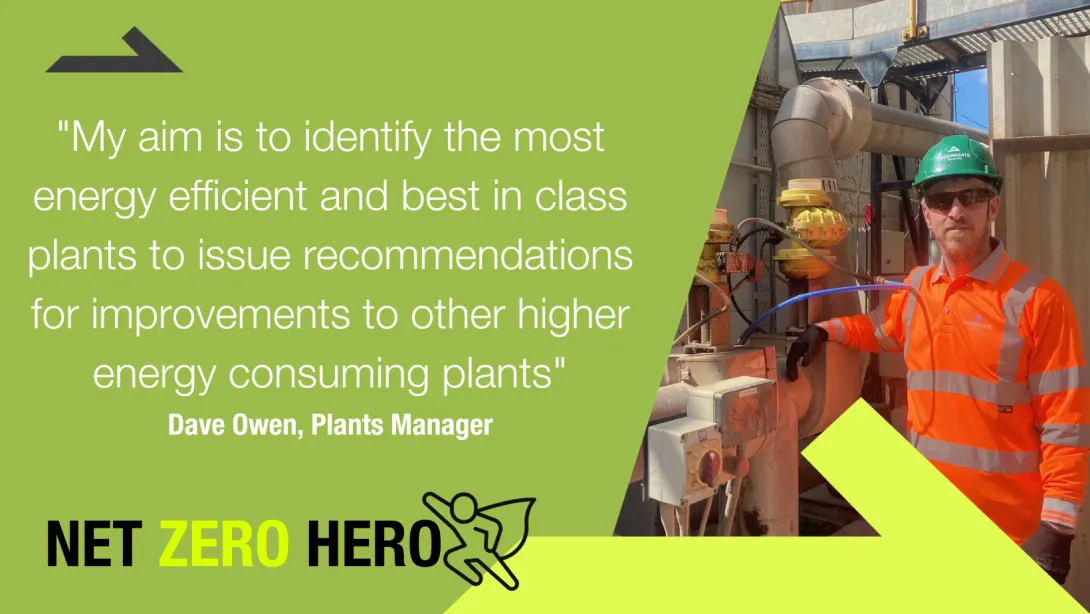
It is often said that some of the best ideas are simple ideas.
And for plant manager Dave Owen it is easy to see how his relatively simple ideas can go on to make big inroads into energy use and efficiency within our asphalt plants across the UK.
Back in 2019, Dave was tasked with looking at ways to save energy at the Astley Plant he was based at and he hasn’t stopped to look back since.
Initially, he analysed the available energy data at his plant and working with team members and electrical contractors he was able to identify a number of ways to make a positive impact and make the plant more energy efficient.
Dave realised by looking at the data that there were a number of pieces of equipment that were run continuously throughout the day which in practice didn’t need to be.
Inverters were fitted on a number of motors on items like bitumen pumps and mixers which meant power could be regulated so that there was only output when equipment was required to be operated.
Dave said: “The changes saved 0.5KW of electricity per tonne, which seems like a small saving on the face of it, but if we replicated this across all of our sites nationwide, it could result in significant savings of millions of kilowatts of electricity every year.
“This not only provides a cost saving but saves electricity and, in some cases, reduces carbon emissions output.”
Not stopping there Dave decided to look at how energy efficiency compared across all of Aggregate Industries’ asphalt plants to see if there was any good practice that could be identified.
He found huge variation between comparable sites on energy use with cost per tonne fluctuating from 80p per tonne right up to £6-£7 per tonne.
So he decided to work out a plant’s baseload - the energy a site uses even when it is not operating- and from that look at ways energy usage could be reduced or made more efficient.
Again, there were huge variations between plants, with some using twice as much energy as comparable sites. The reasons for this will vary from site to site and may be as simple as adding timers to bitumen tanks so they are only heated at night, or reducing the storage temperature of bitumen.
When carrying out a survey at Sheffield, it was discovered that the site was lit by over fifty 500W halogen floodlights. These are now in the process of being replaced by 100W LED lights which will result in a significant reduction in energy use.
Dave added: “These are really simple changes which can be easily put into practice and immediately save energy.
“It would be great to replicate similar actions at our asphalt plants nationwide. We have found that by implementing the measures at Sheffield it can save £18,000 a year alone in energy costs.
“My aim is to identify the most energy efficient and best in class plants to issue recommendations for improvements to other higher energy consuming plants.”
Dave has presented his ideas to the business' Energy Efficiency and Demand Management Group, which was set up as one of five working groups as part of Aggregate Industries' Net Zero strategy.
Press contacts
-
Telephone
01530 510066
-
Email
“These are really simple changes which can be easily put into practice and immediately save energy."
- Major framework win for Surfacing Solutions in Scottish capital
- Aggregate Industries launches the industry’s first carbon reporting tool to offer customers accurate carbon data by product or project
- Aggregate Industries launches ambitious 2030 sustainability strategy: Building Progress for a Sustainable Future
- Innovative SuperLow Carbon wins top industry award
- Aggregate Industries expands its low carbon concrete product range with the launch of ECOPact Prime AS
- Aggregate Industries switches to warm mix asphalt as it continues with sustainability pledge